◇◆ アクリル板のオーダーサービスを使って、ビバリウムを作ろう ◆◇
◇このページについて/About this page
▽材料、道具
▽板取
▽組み立て
▽前面吸気口及び、排水口の製作
▽細部の補強、スライドレール取り付け
▽アルミパンチングボードの取り付け
▽細部の工作:敷居すべり、穴開け、天板のアルミ板貼り
▽ガラス戸と隙間テープ、あと失敗したときの誤魔化しかた
▽細部の磨きのこと
▽終わりに
このページについて
(>>menu)
ビバリウムの作り方。セミオーダーのカットサービスを利用して、アクリル製のビバリウムを作ろう、というページです。なにか一つのビバリウムの製作を追ったものではなく、複数のビバリウムの写真が出てきます。あくまで個人的な作り方のまとめなので、参考に留めてください。
ところで大前提ですが、作ってみて思うのは、「既製品を買ったほうが結局は安上がり」ということです。あと、写真で紹介していあるような前引き戸式の構造には、アクリルはあまり向かないですね。直角にアクリル材を貼り合わせるとか、アルミアングルを貼り合わせるとか、かなり補強しないとゆがみが生じてしまいますから。まぁ、「こういうのを作って、なんか微妙だなぁと思った人がいる」という記録のようなものというこで、ひとつお願いします。どちらかというと、自作するならば『アルミフレームと低発泡塩ビ板を使って、大きくても軽いビバリウムを作ろう』をオススメしたいです。<早く書きなさいよ
設置するのも含めて誰かに手伝ってもらえるなら、大きいものでも、ガラスの製品を購入するので問題ないはず。また、大きさが450*450*450mm、あるいは450*450*600mmぐらいまでであれば、独りで設置することも可能でしょうから、これまた自分で作る意味は薄いです。管理人にも普通にガラスの製品を購入して、内装だけ作っています。これが一番です。あるいは、せめて既製品を改造するとかがよいでしょう。『ガラス水槽を改造して、ビバリウムを作ろう 』をご参照ください。
全部自作しようというのは、何かと工作失敗や、欠陥が後々判明することもあり、そうしたリスクを全部自分で背負わねばならず、面倒なことこの上ないです。
それでも敢えて作ってみた、というのがこのページです。
ところで、それほど大きくないものの場合、ガラスで作ったほうが何かと有利です。前引き戸の扉とか、どうせガラス切って貰うわけですし、一緒にガラスも切って注文しちゃえば、あとは組み立てるだけのプラモデルのようなもの。楽々です。そのほうが工作難易度は下だし、設置する場所も選ばない筈です(アクリルは平滑でない面や平行でない面に設置すると、だんだん歪んでしまいます)。
では何故あえてアクリルで作ったか、というと、これは管理人に腕力がぜんぜんなく、大きいものをガラスで製作した場合、ひとりで移動、設置をするには、ガラス製では無理だったからです(内装含め移動するとなると、限界で450mmキューブぐらい)。管理人の場合、誰かに手伝って貰うという選択肢はなく、常にひとりでやるという前提なので、大きいものを作りたいと思ったとき、ガラスでは難しくなってしまったのです。
実は、自作であるとしても、誰かに設置や移動を手伝って貰える予定ならば、アクリルで作るのではなく、ガラスで作ったほうが、メリットは多いと申し上げておきましょう。コストも、そのほうがたぶん安く作ることが出来ますし、アクリルにつきまとう諸々の問題が、ガラスにはありません。
アクリルで作ることの利点はたった一つ、”軽さ”、それだけであり、それ以外の点では、ほぼすべての面でガラスに負けます。軽さを重要視するか否かで、アクリルで作るか、ガラスで作るかが分かれると言えましょう。
というわけで、今回は軽さ重視のアクリルで作ってみよう、のコーナーです。先述しましたが、ガラスで作ってみた『ガラス水槽を改造して、ビバリウムを作ろう 』も併せてどうぞ。
ヤドクビバリウムを想定しているので、多湿環境で使用すること、上から蛍光灯などの照明を当てることなどを考えると、板はキャスト板を使うべきです。実際作ってみて、今後はキャスト板かな、と思います。でも、コストの関係で押し出し板で作っちゃていますが。
製作してみて思ったのですが、ガラスの前引き戸と同じような構造にするならば、5mm厚アクリル板で製作するのはかなり無理です。横が長くなればなるほど、あるいは前面開口部の高さが高くなればなるほど、分厚いアクリルである必要が出てきます。
アルミアングルをシリコン接着するなどして固定することを前提にするなら、5mm厚アクリル板でも750mmぐらいまで、開口部の高さは400mm以下ぐらいならば作れるでしょうか。個人的には、出来れば接着面のない前面開口部にあたる側面と底面は、8mm厚板が安全だと思います。これはたわみが理由なので、四方を接着してしまう背面は、5mm厚でよいかな、と思っていますが。厚みを8mmにすると重量的な利点はだいぶ消えてしまいますが、それでもまだ5mm厚ガラスよりは軽くなります。
アクリルはガラスとちがって柔らかく曲がるため、前面引き戸型の構造だと、設置場所が歪んでいると、応じて全体が歪み、引き戸に隙間ができてしまうことがあります。これを避けるには、ちゃんと平滑な棚に設置すること。それが出来ない場合は、前面引き戸であっても前面の両脇にL字アルミアングルか、アクリルの板を張り付けて補強材とすることです。
幅900-1000mmを超える場合には、何かしら構造的な補強が必要です。家庭で制作する場合にはアルミフレームがオススメですが、可能か不可能かで言えば木造の何か、たとえばチェストなどにアクリルを打ち付けてシーリングするという方法でも制作は可能でしょう。
実は一番確実な方法は、前面を刳り貫いた板とすることです。ただ、これは綺麗に作るには専用の工具が必要で、理想的にはレーザーカットするべきです。高くつくから現実的ではないですね。
大きいサイズのケースを作ろうとすると、ガラスよりもアクリルで製作したほうが組み立ての難易度が高くなってしまうのは、ガラスが自重で殆どたわまないのに対し、アクリルは柔らかいので、力を加えて「曲げた状態で」接着できてしまうこと、ガラスはシリコンで接着するため、ジグや固定がしっかりしていれば、全体の歪みなどはそこで吸収してくれるのに対し、アクリルはそういった余地がないことから切断精度が組み立てに大きく影響することなどが理由です。特にアクリルは、溶剤で接着してしまうため、偏った力が加わっていると、偏ったかたちに歪んで接着できてしまいます。(あくまで組み立てだけの話で、組み立てたものを移動する方法などを考えると、個人的にはそれでもまだアクリルのほうが作りやすいとは思っていますが)。
組み立ては注意すればどうにかなりますが、注意だけではどうにもならないのが切断の精度です。正確に製作する大前提は、板を高い精度で切断すること。工作機械を使ったオーダーサービスでカットしてもらうことです。それから、天井と全面の開口部に填め込む板も含め、全面をズレなく組み立ててから接着することです。
補強材を入れないアクリル単体での大きなケース製作の経験はそう多くはなく、中くらいのものと大きいものを合わせて10個ぐらいしかまだ作っていません。数年前から作ってはいるのですが、大きいものはアルミニウムの骨組みに貼り付けるかたちで製作したものでしたから、参考にならないんですよね………。そうしたそう多くない作った、そしてそれを使ってみた経験として、アクリルであるならばなるべくキャスト板を使うことと(最低でも天板はキャスト板であるか、二枚の押し出し板を向かい合わせで貼り合わせたもの)、カットオーダーで頼むことは絶対条件だと思います(工作機械があるならば、もちろんその限りではないですが)。組み立ての方法については後述するとして、先にも述べましたが、アクリルケースの製作で一番ネックとなるのは、如何に高い精度でカットするかです。プロの方々は大がかりな工作機械を使って、ズレがでないようちゃんと固定して加工しているのであって、機械もないのにそれに挑もうというのは無理があります。450mmぐらいまでは、精度のズレは組み立て時の調整(ズレたぶんだけずらして接着するなど)で工夫できないこともないのですが、それ以上になるとちょっと難しくなるので、任せてしまうことをこのサイトではオススメしています。前引き戸タイプでなければ、まだ大丈夫かもしれませんが、前引き戸式は扉を閉められるかどうかという問題になりますから。(とはいえ、管理人は作っていませんが、前引き戸式に拘る必要性は全然なく、シリコンで蝶番を接着して扉方式にしてもよいと思います)。
製作するケースのサイズが300mmぐらいまでだったら、たしかに管理人も自分で切るかもしれませんね。でも、サイズが450mmとかになると、頼んでしまうでしょう。ずらっと並べたときに隙間無く並べられるか、とかにも掛かってきますし。
実のところ、もともとは自分で切ったほうが安上がりかもしれんし、みたく思ってやっていたのですが、そもそも最初はアクリルカッタで切断してヤスリで磨いてみたり、丸ノコ使ってみて、それを使うためにジグを作り、それだと微妙だったので正確に切り出すために丸ノコ台を作ってみたり、切断面を綺麗にするのにトリマー使ってみたり、それを使うために治具や作業台を作ってみたり、………なんてことをしてみて、気付けば年単位で時間が経過しちゃって、そういう結論に達したのでした。ここまでやる前にこの結論に達するべきだったと思う………。だって、目的はこのケースを使って飼育することにあるのですから………ケースを作ることが目的なのではないわけで…………。
アクリルのカットオーダーには、大雑把に言えば、910*1820mmなどの決まったサイズの板を一枚買い上げ、そこから板取りをするカットを依頼するものと、単純に欲しいサイズのパーツを購入するだけのものがあります。もちろん、後者が高くなりますが、どうせ余った板など自分で加工しようと思えば工作道具だけで数万円が飛んでしまいますから、欲しい板だけを注文するのを個人的にはオススメします。一個作ると、構造的にこうしたい、ああしたい、と変えたい部分が出てくるかもしれませんからね。構造がもう決まっていて、一気呵成に沢山の数のビバリウムを一気に作ってしまおう、と思っている場合には、効率よく板取り出来る部分はそれで注文するのもよいでしょう。
管理人が使ったことのあるネットショップは、はざい屋、アクリ屋、オービターなどでしょうか。
作りたいサイズが決まったら、材料を揃えていきましょう。
材料及び使用工具
(>>menu)
・アクリル板(どこかの面が、縁に補強材を入れない、開放になっている構造の場合は、板厚は8mm以上が安全でしょう)
底面板:横幅*高さmm × 1枚
側面板:奥行き*(高さ-板厚)mm × 2枚
背面板:横幅*(高さ-板厚)mm
天板:奥50-100mm*(横幅-板厚*2)mm、手前50-100*(横幅-板厚*2)mm、他,補強部材を適宜
前面上部:70-100mm*(横幅-板厚*2)mm、15*(横幅-板厚*2)mm
前面下部(吸気口):50-100mm*(横幅-板厚*2)mm、50*50mm × 12枚
・ガラス戸レール(アルミ製、ABS樹脂製など、好みで)、敷居テープ
・塩ビ管ストレートジョイント(13mm)
・アクリル用接着剤(アクリサンデー)、塩ビ用接着剤(液体タイプ)、シリコン(任意色)、ポリウレタン樹脂系シーリング材(ボンド ビューシール6909など、適宜)、その他各素材(コルク、バークファイバー、流木、発泡スチロール)
・電動ドリル(11mmマルチドリルビット)
・ヤスリ、紙やすり(適宜)
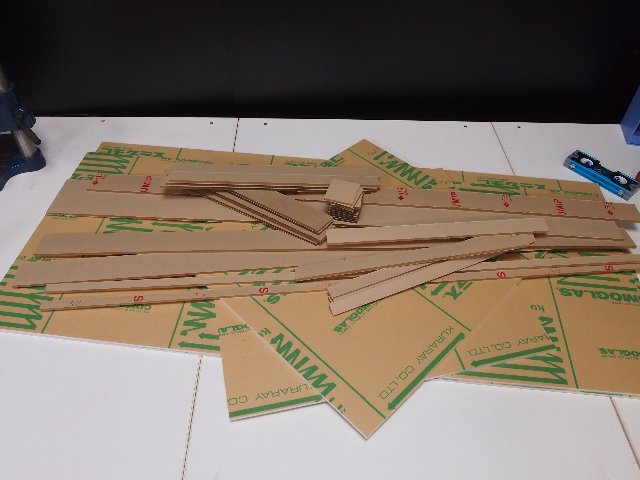
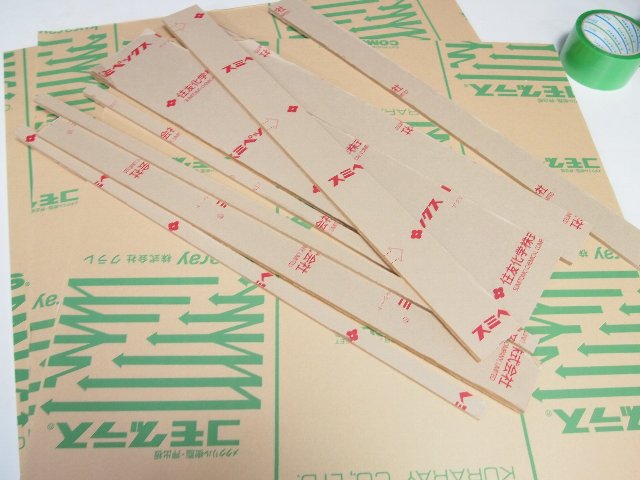
いくつかのケースの材料の例。直線カットは、何かしらの機械を使って切断しないと精度が出ない。カットテーブルやスライドノコがあれば別だが、オーダーでカットしてもらうのが結局は安上がりな気がする。もちろん、工具と技術があるならば自分でカットしてもよい。管理人はスライド丸ノコとかあるので、けっこう自分で切っているけれど、機材の代金が相殺になるのに十年はかかりそうな気がする……。長い板材を押し出し板で用意する場合は、写真のように矢印の方向に対して垂直方向にカットする。大きな板を一枚買い上げて、それを板取する方法でカットを依頼するのが確実だろう。小さいパーツをそういう風にカットしてくれるよう依頼できるかどうかは、ショップにより対応は違うと思うので、ケースバイケースだとは思う。
■板取り
(>>menu)
前面吸気型のビバリウムは、照明などによりケース内部が暖められると、空気が軽くなって上に流れ、結果、前面底部にある吸気口部分から、新しい空気が入り込むという構造で、空気が澱まないため、ヤドクガエルを始めとする多くの両棲類には適しています。彼らは多湿を好みますが、空気が澱むとすぐに死んでしまいます。
前面吸気型ビバリウムにも欠点はいろいろあるのですが、メンテナンス時の利便性の観点も含めると、無難な構造ではあるかな、という気がします。これを使ってみた上で、環境を把握してから、いろいろなものを試してみると良いのではないでしょうか。
今回のものは、少々高いところ(ほぼ目線の位置)に置くので、引き戸か観音開きの必要があり、まぁ引き戸のほうが作りやすそうだな、ということで引き戸を作ることにしました。
構造的には、底面と背面、両側面が一枚の板で、前面は上下に板、上面は、手前と奥にそれぞれ一枚ずつで、手前から奥へ向かって垂直に交差するように素材を組み合わせて補強します。
幾つか作ってみた結論として、管理人は現在では作りたいビバリウムの底面と同じサイズの板を底面とすることにしています。世の中の多くの販売されているビバリウムが、大抵、底面の板の両側に側板がくっついているのは、おそらく組み立てか強度か何かしらの利点があるのでしょう。例えばガラスで作る場合、高さの寸法を揃えるのにはガラスをその高さでカットするほうが楽そうです。なぜなら、下に挟むように接着する方式では、ガラスの自重でシリコンを押し出してしまうであろうことが容易に想像できるからです。側面貼り付けのほうが、下に敷く部分のガラスのサイズを少し小さいサイズにカットしておくことで、決まった量のシリコンの厚みで接着できることになります。これならば、高さが不揃いになることがなく、横幅についてはシリコンの厚みを調整することでぴったりに作れます。
ですが、これらはガラスの話であり、溶剤で接着するアクリルではそれらの誤差を計算する必要はなく、いまの処、この構造で困ったことはありません。
次に、側面と背面の板、どちらを小さくするかは判断が分かれるところですが、これも底面と背面を組み立てるときに両端を板の厚さちょうどずつずらすというのは何かと難しいので、側面の板を小さくしてしまうことにしています。ただ、奥行きと高さが450*450である場合、底面が450*幅であるのに対し、背面は450-板厚*幅になるので注意が必要です。もしこれを間違えて貼り付けてしまうと、けっこう悲しいことになります(やったことがあるらしい)。これはもう気を付けるしかないのですが、どうせ高さ450mmのものなど市販されているのですし、500mmとか600mmとか、背の高いものを作ってしまえ!というのも一興かと思います。それなら短辺と長辺を取り間違えようがないですからね。
例えば、このページに写真がよく出てくる1070*450*500mmの場合では、
底面板:1070*450mm
側面板:450*495mm × 2枚
背面板:1070*495mm
としました(写真では5mmを使っていますが、このサイズのガラス引き戸タイプのケースの場合は、8mmで作ったほうがよいでしょう。前面の両脇部分に補強を入れるならば、5mmでも可能ですが)。 キャスト板であれば問題ありませんが、押し出し板の場合は、長辺を板の矢印方向に対して垂直になるように板取をするとよいでしょう。
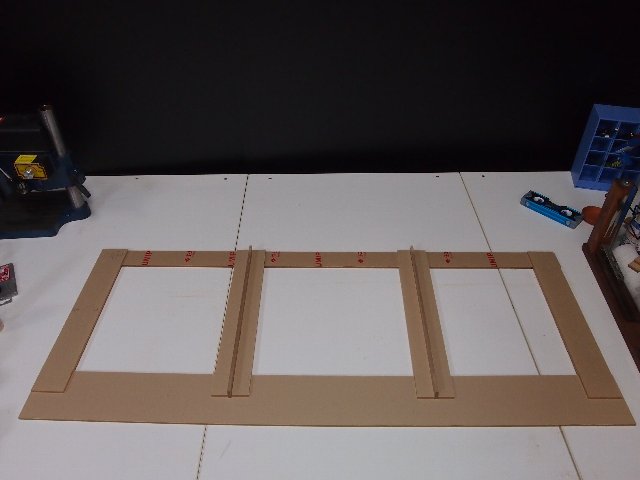
上面のパーツ。どういう構造がベストか、まだよく分からない。5mmの板一枚では、上からの照明の熱と、内部の湿度で、キャスト板であろうと必ずたわんでしまう。そうしたたわみを抑制するべく、板に対し垂直の板を接着したり、二枚貼り合わせたりしているが、正解はよくわからない。
前面は幅を狭くしてしまいたくなりますが、特に上はたわみやすくなる原因になるので、70-100mmはあったほうが良いように思います。下は底面の板があるので50mmでも問題ないような気がしていますが。
精度よく組み立てるために、こうしたパーツは側面の板に対して内側に組み込みます。内側にこうしたパーツを当てて固定した状態で接着したほうが、特に垂直方向にまっすぐ接着しやすいからです。したがって、幅は、ケース全体の幅から板の厚さ二枚分を引いた数値です。
上面手前は、ミスティングを設置するかどうかで変わってきます。個人的には、ミスティングノズルから水滴が落ちることが多いので、ミスティングノズルの直下に吸気口があるのが好みではなく、100mm幅のものを作っています。ただ、上からアクセスするタイプのケースでは、ミスティングノズルをケースの中程に設置してしまうことにして、幅が50mmで作ることもあります。このへんは好みでしょう。
正直、ヤドクガエルのビバリウムにおける上面吸気口の最適な幅がどれぐらいかを管理人は理解していないのですが、おおよそ35-45%で制作しています。このあたりは設置場所、吸気口に使うパンチングボードやアルミメッシュの開口率によっても変わってくるとは思いますが………。大は小を兼ねるではないですが、多少幅広くても、あとからガラス板でも乗せればいいや、ぐらいの適当さなのです。
■組み立て
(>>menu)
固定して、底面、背面、両側面をまず接着します。固定にはいくつかの方法がありますが、今回は外枠となるジグは作らず、養生テープやL時金具、クランプなどで固定して接着しました。
固定具などの道具は、あればそれだけ楽になります。ですが、今回のようなシンプルなものであれば、なければ作れないということもありません。意外と何とかなってしまうものです。でも、道具はなんであれ、あれば便利、なのは確か。一個しか作らないなら、コストパフォーマンスを考えて省略するもよし、沢山作るのならば、道具を揃えてしまうのも良いでしょう。
でも、精度よく組み立てるには、水平な台に対して垂直になる側面の治具はあったほうが望ましいのは確かです。経験上、700ぐらいまでならば、治具なしで組み立てても引き戸の精度はそこそこ出るのですが、900ぐらいから厳しくなる気がします。ただ、アクリルケースではその材料そのものがジグとして使えますから、養生テープだけでもけっこう行ける気がしますが。
薄い板を使っている場合、そもそもアクリル板の自重でたわんでしまい、板が直立してくれません。小さいケースであれば、無視できるレベルなのですが、大きくなるとそうも言っていられません。
これによる組み立てミスを軽減するために、管理人は全面を組み立ててズレがないかどうかチェックをしてから接着することを好んでいます。また、板の固定は基本的には養生テープのみで行い、これも数センチおきに細かく接着し、端だけではなく、少し奥までテープを貼って、引っ張るようにしてテンションをかけて貼り合わせます。テンションは、あくまで板の自重によるたわみが無くなる程度の力です。かけすぎると、全体の歪みがいつまでたっても解消されないからです。いくつか作ってみて、今のところ、固定具を使うよりも、この養生テープによる組み立てが一番精度よく出来るような気がしています。
接着は一般的なアクリル接着溶剤(管理人が使うのはアクリサンデー。というか、これしか知りません)。すぐにくっついてしまうので、手である程度固定して、ということも出来ると言えばできます。ただこの大きさになると、難しい気はしますが。
L字金具とクランプは、端にしかつけられない関係上、たわみやすい素材では自重で辺の中央あたりでゆがみが発生してしまうのを防げません。自重によるたわみが殆ど無視できる、ガラスのような素材では、L字金具や角クランプによる組み立てがかなり有効だったのですが、アクリルの薄い板ではその方法は有効ではない気がします。
写真ではクランプなどと併用してしますが、現在では、むしろ養生テープのみで組み立てるのが一番やりやすいと考えています。板を外側から押さえるのに、ブックスタンドや雑誌を使うことぐらいはありますが。手間がかかるので量産には向きませんが、ちょっとずつ調整すればちゃんと組み立てられるのがよいところです。ただ、そうだとしても、右の写真のように、幅の細い板を垂直方向にクランプで押しつけるように固定すると、開放部分のパーツのたわみを抑制できて、組み立てが少し楽になったりはするので、あればあったでやっぱり便利なんですけどね。
ここでちゃんと組み立てないと、引き戸タイプのケースでは、扉が綺麗に閉まらなくなってしまい、後で調整しなくてはならず面倒になります(精度が出なくても、まぁ工夫次第で運用可能ですが、やっぱりちゃんと組み立てたいですよね)。
内側から押したり、養生テープを貼り付けてひっぱったりし、全体に綺麗に揃えていく(左)。
写真(右)では前面上部のパーツを組み立ててしまっていますが、いろいろ組み立ててみて、先に大きいパーツを接着してから組み立てるほうが精度よく出来るような気がします。
ただ、前面のパーツと、その下に取り付けるスライドレールの台となるパーツぐらいは、最初に組み立てしまったほうが楽かもしれません。あとでケースを引っ繰り返したりしながらこのパーツを接着するのは面倒ではありますから(ただ、面倒でも精度が一番重要だとは思います。この程度であれば精度には影響しないと思うので、そうしてもよかろうと判断しているだけです)。前面上と下にパーツをあてて、丁度良く固定できているようだったら、溶剤を流し入れて接着します。
これはテープでぐっと押し当てていればいるほど起こりうることなのですが、圧迫している場所には溶剤が上手く入り込みません。なので、一回接着した後、二十分ぐらいおいてしっかり固まってから養生テープを剥がし、内側と、それから外側からもう一度接着すると確実な気がします。
どのような組み立てが一番良いのか、試行錯誤していた頃の写真です。
アクリルの項目でも書きましたが、押し出し板を使うときは、上面が内側になるようにして組み立てることにしています。これが正解かどうかは分からないのですが……。
それはさておき、補強部材や天井部分のパーツなど、内側で角の立っているパーツはヤスリがけをしたいところです。
角ばっていると何かと中に入れる生き物のとって危ないかもしれないからで、ケース自体も組み立てが終わったら、角をヤスリがけしていきましょう。トリマーで削ると綺麗な曲面に仕上げられますが、ただのヤスリでも十分見栄えする面落としは可能です。このへんの加工のしやすさがアクリルの良いところですね。
天井の構造はいろいろありますが、どんなものがよいのかは、まだ答えがでません。天板は5mm板では熱や湿度で反りやすいので、二枚の板を裏表で貼り合わせるほうがよいような気がしますが、溶剤で接着する方法では30mm以上の幅の板を綺麗に貼り合わせるのは難しいと思います。そこは妥協するか、あらかじめ10mm厚の板で作るか、30mmぐらいの板を、板の両端に接着するか。いろいろな方法があると思うので、好みのものを選ぶとよいでしょう。個人的には最後のものをオススメします。
■前面吸気口、排水口の製作
(>>menu)
前面は50mmの板ぶんだけ吸気口とするのを好んでいます。レールが乗る分だけ、通気口は狭くなるから、実際は38mmといったところでしょうか。今回はレールにアルミを使うということもあって、手前には足を用意しませんでした。この間のサイズがどれぐらいがよいかは分からないのですが、経験上、100mm弱ぐらいで作ることが多いです。もうちょっとあっても良いかも知れないですが、どちらかといえば、ここに貼り付けるアルミパンチングボードの長さの規格から逆算して、100mm以下の数値にしている感じです。例えば足と足の間隔が90mmであれば、間隔はみっつで290mm。一般的な300mmのものからパーツを取りやすいです(実際は、さらに隣と並べるので、端からならば288mm、間ならば285.5mmといった感じになるだろうか)。もちろん、見栄えを考えて、例えばシンメトリーになるよう幅を調整してもよいと思います。
制作するサイズが決まっている場合、この長さの板を作ってしまっておけば、それに当てて制作するだけなので組み立てが簡素化されます。
さて、前面の板に排水口を取り付けたいならば、前面の板を組み立てるよりも前に加工してしまったほうが楽ですから、その加工をしましょう。
といっても、管理人は殆どのケースを、前面排水口にしていません。殆どのケースは下部に排水口をつけていて、それの下に雨樋タイプの排水経路を設置してあります。これは、接続してしまうと、ずらっと並んだケースから一つだけを取り出すときに凄くたいへんだからです。あと、排水系を接続しないほうが伝染力の強い感染症への対策として心持ちよいという話を聞いたことがあるから、というのもあります(まぁ、ミスティングシステムのほうは繋いでいるので、それこそ気は心かもしれませんが)。一番大きいのは、前面の見える場所に配管があると、見栄えがなんか好きではない、というのも理由のひとつでしょうか。
いくつかある前面排水タイプのケースの横に並べるものだったら、そういう加工をすることもあります。
塩ビパイプを接続できるように、内径13mm用の塩ビジョイントを、中央よりも5mmほど余裕を持たせてカット。
ヤスリに擦り付けて、平面を綺麗にしましょう(左:上に見えるのがヤスリで削った面)。写真ではなんかそれ用っぽい平面のヤスリを使っていますが(ドレッサーといいます)、角材にサンドペーパーを巻き付けて、折り曲げたところでガムテープで留めたものとかでも同じことができます。240番目だと荒いから、仕上げは400番か500番ぐらいのがよいのではないでしょうか。
続いて、前面下部になるアクリル板にドリルで穴をあけます。大きい穴をあけるのは難しいですし、ある程度の大きさの穴をあけたら、あとはヤスリで広げてしまうほうが簡単かもしれません。もうちょっと大きいヤスリでやりたかったのだけど、なんかヤスリがこのときは見当たらなかったのです(整理整頓は大切ですね)。
アクリル用と塩ビ用の接着溶剤を等比で混ぜたもので接着しましょう。要領はアクリル板などを接着するときと変わりません。ただ、ヤスリがけをした面はやや荒いので、しっかりと溶けるようにして接着したほうがよいですね。できれば、接着面がよく溶けていることが確認できたらクランプで固定してもよいかと思います。
■細部の補強、スライドレール取り付け
(>>menu)
だいたいの接着が終わったところ(左は1070*450*500mm,右は550*600*550mm。左は前面上部が50mmしかないが、これだと部材の強度が低く、歪みが起きやすいので、現在は右のように100mmにするのが正解かな、と思っている。)。
接着が上手くいっていれば、これで水漏れはないのですが、やはりそう上手く行かないこともあるものなので(経験者は語る<たんにヘタなだけでは?)、角に三角棒を入れておきましょう。シリコンでシーリングするのでもオーケイです。このへんはお好みで。
長さは大まかにカットしたあとはヤスリで調整していきます。角棒でもよいかと。
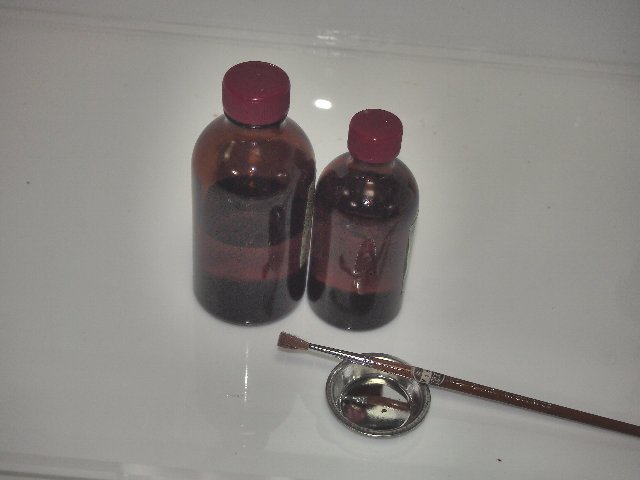
金属用のプライマーと、プラスティック用のプライマーは、それぞれ異なるものなので、二つ必要になる。写真はラベルを剥がしてしまったが、信越化学が出している金属用のプライマーCと、プラスティック用のプライマーT。セメダインなどには、金属とプラスティック両用のプライマーがある。
今回はアルミのレールを使用します。何故か?管理人はアルミが大好きだからです!(それ以外の理由はないです)。 まー、さほど好きでもないなら、PVCでも良いんではないですかね?(なげやり)
冗談はさておき、PVCのほうがメリットはあります。というのも、アルミは、ビバリウムのような常時湿度が100%に近く、また酸性になりやすい環境下では、切断面などのアルマイト処理のされていない部分が腐蝕してしまうことがある、 という注意点があります。欠点とまでは言えないのは、ハヤコートやラッカーでコーティングしたり、そもそも切断面にあたる両端のところはシリコンで埋めるようにすれば、実用上問題にならないからです。まぁ、ちょっと一手間掛かるのは事実ではありますが。
シリコンは、最近は信越化学の信越シリコーンを愛用しています。たぶんプライマーは必要ないとは思うのですが、今回は長期間使うのだし、特に前面は力が掛かる可能性があったので、プライマーを塗布しました。話を聞く限りでは使わなくても問題はないような気がしますけどね。そもそもこのプライマーは、それなりに力が加わる可能性があるな、と思う別のものを作るときに購入しただけのものなので………。
今回は、レールを接着してからアルミパンチングボードを接着。そのほうが、前から見たときに見栄えがよいから(アルミの板の上にレールだと、横から見たらアルミ板の厚みが見えてしまうのですね) 。アルミが好きだから、という理由は本当ですが、一応、アルミだと硬度があるので、安心して橋桁スタイルの前面吸気口に出来るというのも理由ではあります。
■アルミパンチングボードの取り付け
(>>menu)
力のかからない部分、例えばアルミパンチングボードの部分には、プライマーの必要性を感じなかったのでつけていません。適度に手を抜いていきましょう。
前面吸気口のアルミパンチングボードは、φ1P2、つまり穴の径が1mmで、ピッチが2mm、60℃千鳥格子の、厚さ0.5mmのもの。東急ハンズに注文すると、600*400のサイズでも取り寄せてくれるので、好んで使っています。東急ハンズではA-8という表記になっていますが、このコードの意味はよく分からないですね。アルミパンチングボードと、下の足との接着が終わったら、アルミレールとアルミパンチングボードの隙間にもシリコンを入れて接着。シリコンが固まる前にマスキングテープを剥がすのだから、アルミパンチングボードがしっかり接着してからでないと、この作業はできないわけで、つまり別の日にやっています。けっこう日数がかかるのです。まぁ、内装と平行して進めても良いのではないかと。
ところで、アルミパンチングボードを接着するとき、アルミの穴からシリコンがニョロニョロのように出てくる(ムーミンを見てください?)。これをどのタイミングで切り取るか、というのは難しい問題です。好みの問題ではあると思うのだけれど、現時点ではすぐにカッターナイフで取り除いてしまうことにしています。これは、上手くやればそのほうが綺麗に仕上がるからですが、もっと上手いことやる方法はないものか、というのは気になるところです。固まってからカットすれば、まちがって埋めたくない隙間にシリコンを押し込んでしまう心配はないが、どうもささくれたように切れてしまうこともあるような気がするのです。尚、接着前に前面の細長いパーツの角のところはヤスリがけをしてあります。
■内装:敷居すべり、穴開け、天板のアルミ板貼り
(>>menu)
写真では内装も平行して進めてしまっていますが、そのへんはお気になさらず。 スライドレールに、ガラス引き戸が滑りやすくなるよう、すべるテープ貼り付けします。必須という訳ではないですが、管理人入れるのを好んでいます。写真は敷居用のもので、両面テープが既に貼り付けられています。これをスライドレールの幅にカット(だいたい、出っ張っているところを両端にして、四山ぶんです)。凹凸に合わせて切ればよいので、長くてもけっこう簡単です。
設計上問題ないと分かっていても、最初に作る寸法の場合、ガラス戸にするガラスの高さは、実寸を測ってからオーダーするのを好んでいます。端材のアクリル板などを差し込んで、どれぐらいだったら差し込めるかチェックします。高さと幅が決まったら、オーダーガラスか、ガラス自販機さんあたり、もしくは近所のガラス屋さんにお願いしましょう。引き戸の重なり合う幅は、20mmは欲しいところです。
ただ、これだと割高ですね。同じ寸法で同じ素材で作っている場合は、複数枚注文すると割安になることもあるし、そうでなくても送料分がお得なので、これ!という構造のものを決めたら、それを複数作っちゃうとよいでしょう。
ガラス戸と一緒に、天板のガラスも注文しておきます。あまり意味があるか分かりませんが、照明の直下はガラスにしてみたりするのでした。三等分なので、同じサイズのものを三枚。残りがアルミパンチングボードを貼り付けるエリア。
以前作った天板は、前後を真横に分ける長い板がある構造でした。これにより、奥のほうをアルミパンチングボードにし、手前はガラスにしてフタのように持ち上げられるようにしていた訳です(そんなに高い位置に置くものではなかったからです)。そのときは、天板の手前の幅が50mmで、穴をあけただけでは、ミスティングノズルを上手く設置できませんでした。貼り合わせた部分の厚さは10mmあって、隔壁ユニオンを上手く固定できなかったからです。また、奥のほうにミスティングノズルを設置したい、という場合もあるでしょう。今回は意図的に手前の板を貼り合わせではない構造にしてみたのですが(計算上これで大丈夫ですが、実際に試してみるということで)、天板のほぼ全てのパーツが貼り合わせだった場合は、ミスティングノズルがつけづらいということになります。
隔壁ユニオンのうち、国内で入手できるものの多くは10mm厚でも問題はないのですが、手元のものが5mm厚ぐらいまでのものしかなくて、それをどうしても使いたいという場合や、あるいは天井の板部分が、12mm厚ぐらいの板になっているという場合は、フォスナービットというものを使い、約5mmの深さまで周囲を掘れば、簡単に固定できるようになります(写真右)。 普通のドリルビットでは、先端が鋭角になっているので、外縁部を望む深さまで削ると、中央部分を削りすぎることになります。なので、フォスナービットの登場と相成る訳です。
続いて、アルミパンチングボードを貼り付ける作業をします。貼り付けないほうが後で他に流用しやすくて良いような気がしますが、何かの拍子にズレたことに気付かずにヤドクガエルがでちゃったりしたら悲劇すぎるので、接着してしまうのを好んでいます。ついでに、天板に穴をあけてミスティングノズルをセットしていきます。
■ガラス戸と隙間テープ、補強と、失敗したときの誤魔化しかた
(>>menu)
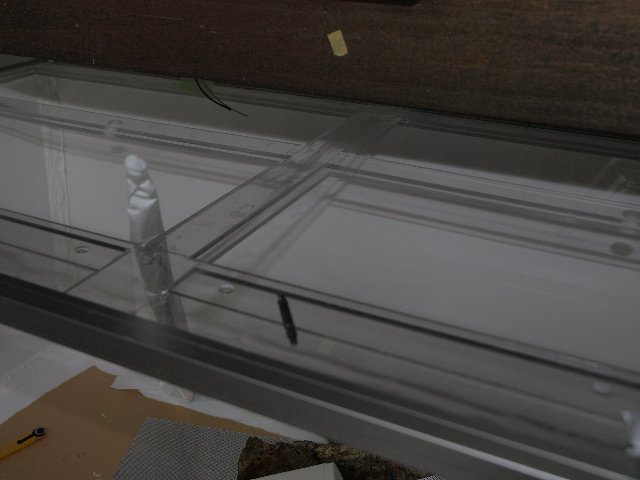
別の時に作ったもの(アルミフレームタイプ)。横板のアクリルを二枚貼り合わせ(裏表)にし、中央に前から奥へ同じような二枚重ねの板を渡してある。やや奥のあたりに、二枚重ねの横の板材を配置し、奥がアルミパンチングボード、手前がガラスのエリア。下に位置する板材を5mm幅ほど大きくしてあるので、手前の空間にはちょうどよいサイズのガラスを乗せるだけで接着する必要がない。ただ、幅のある長尺板を綺麗に貼り合わせるのは難しいので、綺麗に仕上げたいならば別の構造を考えたほうが良いかも。
いろいろ作ってみて思うのですが、引き戸のガラス板には取っ手をつける削り加工を注文すると良いと個人的に思います。これは、一度作ったガラス製のビバリウムを解体して、それぞ加工し、素材として再利用するということが、管理人には殆どないからで、再利用するかもと思うならば、しないのも手ではありますが。とか言いつつ、写真のものは見ての通り、ただのガラス板ですけれども。
再利用を考えるならば、取っ手はゴム製のちょっとしたシールを貼ってもよいですし、加工を施したアクリルなどを両面テープで貼り付けてもよいでしょう。なんにせよ、見栄えに拘るかいなかは個人の趣味かと思います。
といっても、いくら見栄えにこだわろうと、前引き戸タイプのビバリウムでヤドクガエルを飼育しようとすると、案外台無しになるのが隙間テープの存在。普通にガラス戸のままでは隙間からショウジョウバエとかが逃げ放題なので、隙間テープを貼って、ショウジョウバエが外に出ないようにします。まぁこれが見栄えがしょぼくなる最大の理由ですが、まぁ致し方ないですね(苦笑) ショウジョウバエは案外、昆虫ゼリーとかを使うことで脱走を抑制できますが、コオロギは逃げ放題になってしまいますしね。
さて、ケースがちゃんと計画通りに製作されていれば、歪みはなく引き戸も隙間無く閉まる筈です。上手く行ったら、自分の組み立て技術に満足するとよいと思います。
…………とはいえ、上手く行かなかいこともあるかもしれません。っていうか管理人はありました。最近は問題なく組み立てられるようになりましたが。上手くいかなかったときはどうしましょう? 折角ここまで作ったのですから、使えないなんて困ります。もったいないです。どうにか誤魔化して使ってしまいたいところです。
また、先にも書いたように、設置する台が歪んでいると歪んでしまいがちです。分厚いアクリルであれば問題なかったりしますが、薄いもので作っていると確実に歪みがでます。そういう意味では、アクリルで補強部材なしで前面を全部開放して引き戸タイプの構造にするのに、そもそも無理があるってことなのでしょう。
とくに薄いアクリルで作った場合には、歪み無く組み立てられても、湿度による歪みが時間経過で発生しますので、前面開放部の縦の部分に補強が必須になります。ひとつは、アクリルのアングルをシリコンで貼り付ける方法です。これには、歪み無く設置した状態で貼り付けることが肝要です。
この方法は、ちょっと歪んで作っちゃって、引き戸がぴったり閉まらない場合の誤魔化し方としても有効です。
右の写真のように、L字型のアルミアングルを両側に貼り付けます。見た目も、これだと最初からこういう風に作ろうと思っていたんですよ実は、みたいな感じで誤魔化せるのでオススメです。アルミアングルは硬いので、クランプをつけてシリコンで接着することでアクリル板がたわんでしまったりした場合も矯正することができます(度合いにもよるでしょうが)。長さの寸法がしっかりしていれば、むしろコレがあることで全体の補強にもなるでしょう。歪みが補正しきれず、ガラス戸がぴったり閉められないような場合は、アングルの見えない裏側の位置に、隙間テープを貼ってしまえば密閉性も確保できます。
他にも、扉の内側にアクリルの細い板を張り付け、そこに隙間テープを貼るという手もあります。アクリルの板が側面の板の歪みを抑制する補強部材にもなります。端材があるならば、追加費用が発生しないという意味ではお得なのですが、これだと見るたびに、この方法でごまかしてますよーというのが見えてしまって、精神衛生上よろしくないかもしれませんね。L字アングルも、大差ないといえば大差はないですが。
どちらかというと、管理人はL字アングルを貼り付けるほうが好きですが、このあたりは好みかと思います。
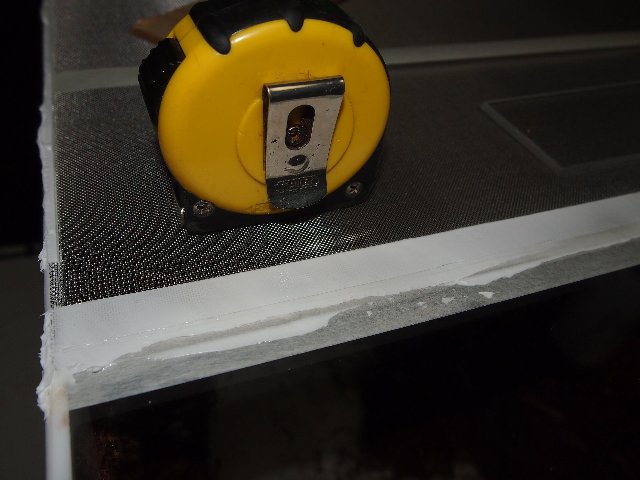
型枠があるならば、二度に分けてやる必要がないかもしれないが、目の細かいメッシュだとテンションをつけて貼るのが難しいこともあって、写真のように端をテープで押さえてテンションをつけ、それから接着してしまうのが網の張り具合の仕上がりを重視するならば確実だろうか。もっと良い方法はないものか、模索の日々。(網が丸みを帯びているので、適度な重さを加えるために上にモノを載せている)
少し話が脱線してしまいますが、アルミパンチングボードではなく、ステンレスメッシュを貼り付けるバージョンの話も書いておきます。別ページでやることもないかな、という気がするので。
写真は600*400*400のケースで、小型ヤモリ用なので#40だったかのステンレスメッシュを貼り付けています(#60だったかな?)。金網はロールで購入するため、丸まり癖がついています。また、丸まり癖がないとしても、ピンと張った状態で接着するのは何かと難しいものです。テンションのある状態で接着するのが良いのでしょうが、どうやればよいのか思いつかないので(ポリプロピレンで枠のようなジグとか作れば出来そうですが、そんなの作るのめんどいです)、管理人は二回に分けて接着することにしています。丸まりが上か下かは好みでしょうが、管理人は丸まりのでっぱりが上になるようにセットしています。このほうがテンションを利かせやすい気がするからです。基本はマスキングテープで丸まりを伸ばすようなカタチでケースにセット。金網のフチもテープで押さえます。余分な部分にシリコンが付着しないように、縁取りもをします。そして、残りの部分に空気が入らないように密着させた状態でシリコンをつけ、ヘラで均します。
テンションを押さえるマスキングの下には、シリコンを付着させられないので、一端これが固まった後に剥がして、もう一度コーキングをすることになります。数時間ぐらいしてマスキングテープの上に乗っているシリコンがほどほど固まったら、端の部分にカッターで切れ目を入れておきましょう。12-24時間ぐらいしたら、マスキングテープを全部剥がし、再度マスキング、残りの部分にもシリコンを塗っていきます。
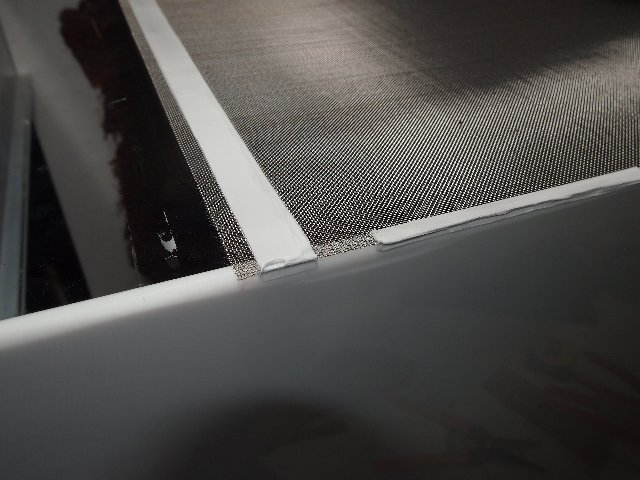
マスキングテープを剥がしたところ。金網のフチに沿って新しいマスキングを施し、シリコンを追加して仕上げる。(マスキングのミスで、シリコンが予定外の箇所に付着してしまっているが、こういう場合はカッターやスクレーパ、もしくはプラスティック消しゴムなどで剥がし、傷がついた場合は研磨材をつけたフェルトホイルで磨けばよい)。
シリコンのカタチを綺麗に仕上げたい場合は、アクリルの端材などにマスキングテープを貼り、それを養生テープなどで固定して、枠のようなものを作ると、シリコンを整えやすいでしょう。ポリプロピレンの板でも同じことが出来ると思います。薄く綺麗に仕上げたいならば、0.5mmか0.8mm厚のポリプロピレン(PP)板を枠にするのがよいでしょう。PPは全く接着しないので。固まってから綺麗に剥がすことが出来ます。構造が決まっていて、いくつも作るならば、ポリプロピレンのそういう型枠を作ってしまうのもよいかもしれませんね。シリコンは平行方向に綺麗に削ぐということが難しいので、見栄えよく仕上げるには、そういう型枠を用意して、平滑なヘラで均すのが一番確実でしょう。
■細部の磨きのこと
(>>menu)
磨いた話でも。接着時に溶剤をこぼしてしまって、白くなってしまったところなども、サンドペーパで均して同じ要領で磨いて(ある程度は)綺麗にすることができます。もちろん、あくまでちょっとごまかせる程度でしかないので、こぼさないのが一番なんですけどね………。
写真の右は、トリマ加工をしたアクリル板の側面を、研磨剤とフェルトホイルで磨いたものです。右側が磨く前、左が磨いた後ですね。磨くと向こうが見通せるようになります。もっともっと磨くことも可能です。向こう側が見えるのまで磨いて、「見えたからなんなの」って言われたら、「ヤドクガエルなんか飼ってどうすんの」って返しましょう。こだわりというのはそういうものですよー。
前面吸気口や、ケースの外枠のフチの部分など、切断面が正面に向くパーツでは、切断面の仕上げがそのまま見た目に関わって来ます。接着面が丸ノコによる切断のままの場合、普通に接着すれば丸ノコの回転と移動により出来た波模様が、そのまま見えてしまうことになるでしょう。これは普通の鋸で切断しても同じです(丸い波ではなく、切断したときのノコの動き、直線が連なることになるだけです)。トリマーは回転するビットにより切断するので(CNCの場合もそうです)、ビットの進行方向に向かって垂直に直線の波がこれまた出来ます。こちらも、接着すると微妙に見えてしまいますね。
でも、磨きすぎるのも考え物で、ぴかぴかに磨き上げたものを接着面にしようとすると、溶剤を綺麗に流し込むのがちょっと難しくなる感じがあるような………均一にごくわずか、板と板を離して、そこに流し込めるならば、問題はないのですが、これもまた難しいですしね。トリマ仕上げのものを接着して、圧迫することで凹凸を無くしてしまおうとすれば、ゆがみが発生しかねません(いずれも、しっかりとした作業場があれば出来なくはないのでしょうが、あくまで机の上で出来るかどうかを考えた場合)。
いろいろやってみた結果、接着面も含め、個人的にはトリマー仕上げで満足しています。加工性も悪くないし、磨けばけっこう綺麗。磨くと言っても鏡面まで磨くのではなく、研磨剤をつけてフェルトホイルで仕上げるだけですが。ただ、トリマ仕上げの場合、全体をペーパがけしたわけではないので、磨いてもトリマ加工の波は見て取れますが、それもよしかな、と。
…………まぁ、このフェルトホイルによる磨きだけでも、けっこう大変なので、最近は殆ど磨いていないのですが(苦笑)
■終わりに
(>>menu)
今回はアクリル板を使っての製作でした。
ネット上では、いろいろな人がいろいろな方法でビバリウムを製作している様子をアップしているので、それらを見て、自分にあった方法で自分好みのものを製作するとよいのではないかと思います。このページは、そのうちのひとつということですね。
規格サイズのビバリウムケースであれば、購入するので全然構わないと思います。管理人も買っています。でも、そうでないサイズのものが欲しい!と思ったときは、作ってしまってはいかが?ということなのでした。皆々様もどんどん作って、ネットのどこかにアップロードするとよいと思います。管理人は、それを見て楽しみたいな、と思う次第なので。いかに素晴らしい検索ツールがあったとしても、ネット上に存在しないものを読ませてはくれませんからね。
それでは、内装編へ続きます。
▼ビバリウムの内装をつくろう (ヤドクガエル編 ポリウレタン樹脂系 シーリング材)
▼ガラス水槽を改造して、ビバリウムを作ろう
(以下はまだ書いてません)
ビバリウムの内装をつくろう (樹上棲ヤモリ編 パテ+防水ニス)
ビバリウムの内装をつくろう (地表棲ヤモリ編 パテ+エポキシ樹脂)